1. What is MgO Board?
Also known as magnesium oxide board, magnesium board, mgo panel, or magnesium oxide panel, it is a fire-resistant building material made from magnesium oxide, fiberglass mesh and other components. Some people refer to it as “mgoboard”, but it refers to the same product. It is widely used in passive fire protection systems for both residential and commercial buildings.
Known for its excellent fire resistance, moisture resistance, environmental friendliness, and non-toxicity, magnesium oxide board is an upgraded alternative to traditional materials such as cement board, gypsum board, and calcium silicate board.
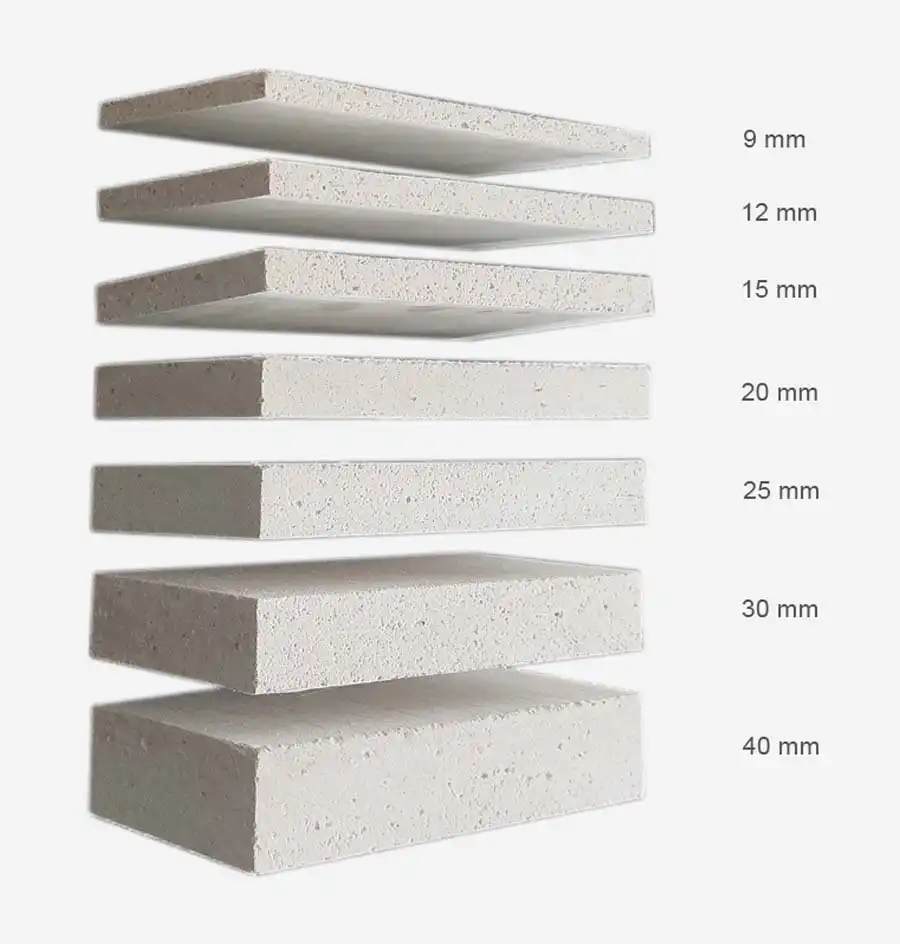
2. Different Types
Magnesium oxide panels are mainly divided into two types based on their chemical composition: Magnesium Chloride Boards and Magnesium Sulfate Boards.
3. Raw Materials
The main raw materials of magnesium oxide board include:
- Magnesium oxide
- Magnesium chloride or magnesium sulfate
- Perlite
- Wood sawdust
- Fiberglass mesh
- Non-woven fabric
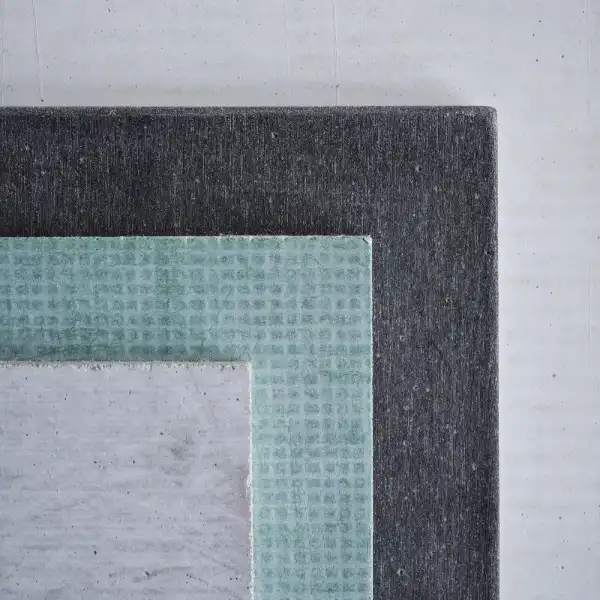
4. MgO Board Applications
It is widely used in passive fire protection systems for both residential and commercial buildings.
✅ Sub-flooring
✅ Fire door
✅ Decorative panel
✅ Acoustic panel
✅ Fireplace
✅ Duct
✅ Kitchen
✅ Laundry room
✅ Office buildings
✅ Hotels
✅ Theaters
✅ Schools
✅ Data centers
✅ Libraries
✅ Highway Tunnels
✅ Interior wall
✅ Sub-flooring
✅ Fire door
✅ Ceiling
✅ Decorative panel
✅ Acoustic panel
✅ Furniture
✅ Fireplace
✅ Duct
✅ Bathroom
✅ Kitchen
✅ Laundry room
✅ Office buildings
✅ Shopping malls
✅ Hotels
✅ Theaters
✅ Schools
✅ Gyms
✅ Data centers
✅ Libraries
✅ Highway Tunnels
5. Specification
The most common sizes are 1220*2440mm (4*8ft) or 1200*2400mm, with the maximum size reaching up to 1200*3000mm (4*10ft).
Since the standard mold sizes available on the market are typically fixed at 1300*2500mm and 1300*3100mm, all other smaller sizes are cut from the 1200*2400mm and 1200*3000mm boards.
Magnesium oxide boards are available in a wide range of thicknesses, typically from 3mm to 40mm, depending on the application.
✅ Wall panels: commonly 8mm, 10mm, or 12mm
✅ Flooring panels: 18mm or 20mm
✅ Ceiling boards: 5mm or 6mm
✅ Tunnel boards: up to 40mm
✅ Door core panels: typically 38mm or 48mm
MgO boards have a density range of 650–1400 kg/m³, depending on their intended use.
✅ Wall panels: typically 900–1000 kg/m³
✅ Flooring panels: 1200–1400 kg/m³
✅ Door core panels: 240–350 kg/m³
The standard magnesium oxide board (mgo panel) features a smooth and flat front surface, while the back side has a slightly rough texture with a fiberglass mesh pattern.
✅ Sanded: The back side is further processed to become smoother and more even. Click HERE to see the differences between regular board and sanded board.
✅ Special treatment: The board surface can also be laminated with other materials such as PVC film to create decorative finishes with various patterns and designs.
The standard color of magnesium oxide panels is white. However, by adding specific additives, other colors such as gray, black, and more can also be achieved.
6. MgO Board Features
MgO board is a next-generation building material known for its durability, fire resistance, and eco-friendliness. It provides an ideal solution for both residential and commercial applications. Key features include:
Magnesium oxide board is a next-generation building material known for its durability, fire resistance, and eco-friendliness. It provides an ideal solution for both residential and commercial applications. Key features include:
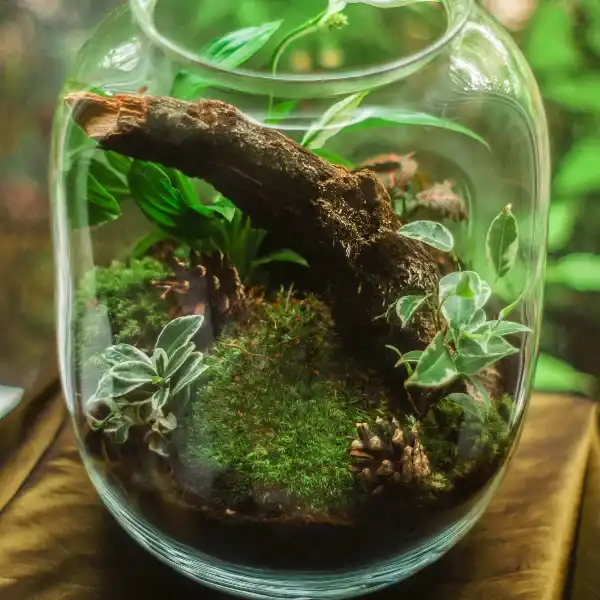
7. Limitations
❌ When used for exterior walls, the boards cannot be directly exposed to sunlight, rain, and wind, as this will significantly shorten the lifespan.
❌ Chloride-based MgO boards, if poorly manufactured — with substandard materials, incorrect formulas, or insufficient curing — and without proper soaking treatment, may develop salt efflorescence in humid environments. This can corrode steel and damage other construction materials.
8. Production Process
The production process of mgo board typically includes the following steps: raw material mixing, board forming, curing, demolding, drying, and cutting.
9. MgO Board Installation
The installation method for magnesium oxide boards is similar to that of other fire resistant boards or fireproof panels. Thanks to their lightweight structure and ease of cutting and screw-fixing, they offer great flexibility during construction.
There are no strict limitations on how to install them—construction teams can apply standard practices or follow their own experience to determine the best approach on site.
Note: An important precaution is to avoid prolonged exposure to rainwater, which may affect the performance of the board.
Below are typical installation methods for interior partition walls and sub-flooring systems, provided for your reference.
10. Packaging
The packaging of magnesium oxide boards typically involves stacking the boards on wooden pallets, securing them with packing straps, and wrapping them with stretch film or plastic bags (customizable with logos). Upon customer request, edge and side protection can also be added.
11. Container Loading
13. Why Did We Create This Page?
There’s a growing amount of information online about magnesium oxide (MgO) boards—but much of it is scattered, inconsistent, or difficult to verify. For buyers, contractors, and new users trying to make informed decisions, this can lead to confusion and uncertainty.
As a professional MgO board manufacturer with over 20 years of experience, Suparna is committed to building a reliable, accessible, and practical knowledge base. This comprehensive guide brings together the key facts, technical insights, and industry practices related to magnesium oxide boards—from raw materials and specifications to installation methods and packaging.
Whether you’re planning a construction project, evaluating suppliers, or simply exploring building materials, we hope this page helps you understand MgO panels and how to use them effectively.
If you have any questions, suggestions, or need further details, feel free to contact us directly. We are always here to support your project and continuously work to improve this resource.